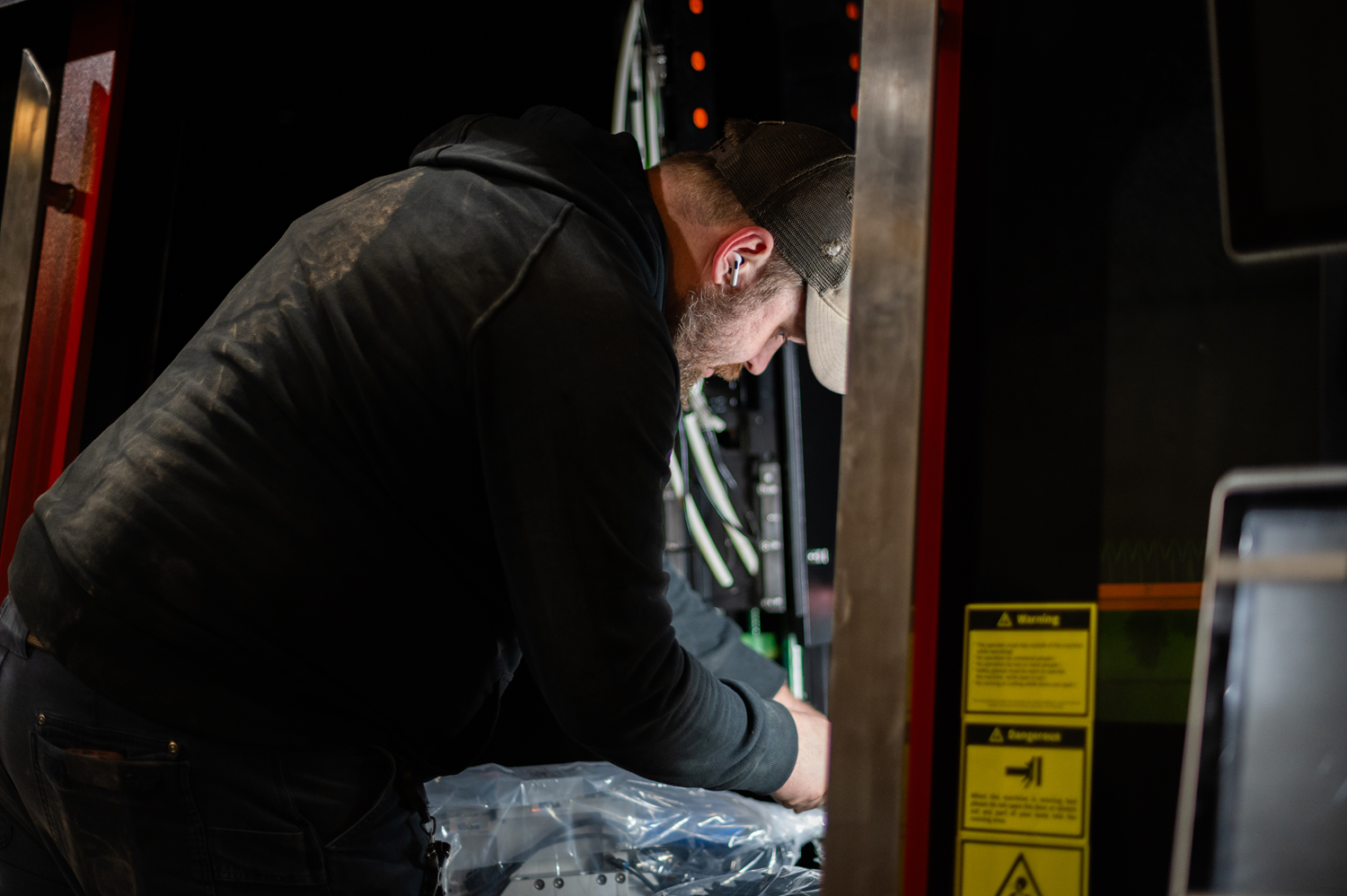
Machine preventative maintenance often falls to the bottom of a manufacturer’s list, and it’s easy to see why. During preventative maintenance, the machine is not productive and, therefore, not making money for the manufacturer. Also, costly machine repairs are often found during preventative maintenance, which require additional downtime and money. For example, when a press brake is down for preventative maintenance, it is not bending parts that can be shipped out. And if there is an issue found with the light curtain, additional downtime is needed for repairs.
In spite of these preventative machine ‘cons,’ there are many reasons---or ‘pros’---that should make a strong machine preventative maintenance program a top priority. In the press brake example, finding the light curtain issue during preventative maintenance, and the prompt repair of it, can significantly reduce the risk of a costly workplace accident and issues with bending quality during operation.
Reduces Downtime
While checking off all the items on a full preventative maintenance list requires scheduled downtime, it can lead to less unexpected downtime in the future. Simply, if issues are found earlier, then they won’t break suddenly during operation. Sudden breakdowns and part failures lead to costly delays in production that can dramatically impact a shop’s production schedule.
For example, an OpEx service engineer was called in because a laser was not cutting straight. The problem turned out to be a belt that was so worn it broke in his hands. If the issue had been found during preventative maintenance, it could have been caught before impacting quality and productivity.
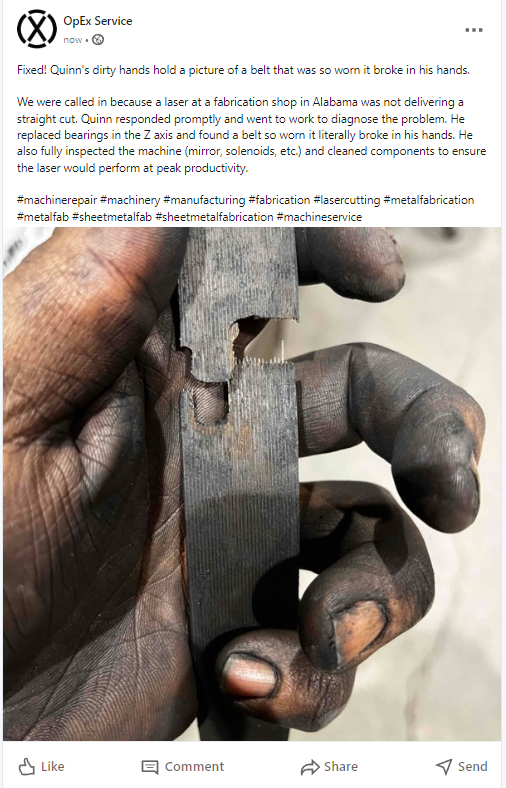
Extends Equipment Lifespan
With regular inspections, lubrication, fluid changes, and all the other tasks associated with preventative maintenance, a machine can last longer and decrease a manufacturer’s need for new equipment. By keeping equipment in optimal condition, companies can defer the need for expensive machine replacements and maximize the return on their initial equipment investment.
Boosts Machine Efficiency and Performance
Regular preventative maintenance not only ensures that machines can run longer, but also increases the likelihood of them running at peak productivity and efficiency. The latter ensures that the machine’s energy consumption is optimized, which means lower operating costs throughout the life of the machine.
When all parts are proactively replaced before failure, a machine can also perform better, in terms of quality and precision. This translates into less material waste, less part “re-dos,” and less production schedule delays. In short, enhanced performance contributes to smoother operations and higher overall productivity.
Decreases Risk of Costly Workplace Accidents
According to the National Safety Council, workplace injuries cost employers $167 billion in 2022. When equipment is operating correctly and all safety features are in good repair, the risk of costly accidents significantly decreases. Regular preventative maintenance inspections can identify potential hazards, such as malfunctioning safety features or worn-out components, before they pose a risk to workers. By addressing these issues proactively, companies can prevent costly accidents and maintain a safer workplace.
In addition, regular preventative maintenance helps ensure that all equipment meets safety compliance requirements. If a workplace accident does occur, safe, well-maintained machines can help companies avoid potential legal issues and fines.
Reduces Overall Repair Costs
While it may seem that preventative maintenance equates with more repair costs (because worn parts are found during PMs), preventative maintenance can actually lower repair costs in the long run. By catching and addressing small issues before they become major problems, companies can avoid expensive emergency repairs and the associated downtime.
Neglected and worn parts can also lead to increased wear on other parts and even sudden catastrophic part failures. In short, it takes less time and is less expensive to replace one worn part than a whole system.
Improves Equipment Reliability and Builds Trust
Preventative maintenance supports operational reliability, which is vital for meeting contractual obligations and maintaining high service standards. Reliable equipment is a crucial part of that, ensuring that production schedules are kept, deliveries are prompt, and customer trust is maintained. This can contribute to a positive company reputation and opportunities for growth.
Operational reliability can also have a positive impact on employees too. When employees are not constantly dealing with equipment failures or safety concerns, they can focus on their work and contribute more effectively. Moreover, knowing that their employer prioritizes a safe and functional work environment can boost morale and job satisfaction.
Conclusion
Preventative maintenance may come with downtime and repair costs, but its benefits are undeniable. By reducing downtime, extending equipment lifespan, boosting machine efficiency and performance, decreasing the chance of workplace accidents, lowering repair costs, ensuring compliance, and improving equipment reliability, a strong PM program proves to be an invaluable strategy for maintaining a smooth and productive industrial operation.
Obviously, it’s not always easy to get preventative maintenance done on schedule, especially when staffing is low, or employees are tied up with facility maintenance and equipment repairs. In these cases, it can be beneficial to bring in a knowledgeable maintenance service with experience with all brands and types of machinery.
A robust preventative maintenance program not only enhances the operational efficiency of machinery but also contributes to overall business success. In the end, proactive equipment care can go a long way in securing long-term gains and sustainable growth.